With ERTÜRK quality starts right at the beginning of the process. This for us is the raw material. We as ERTÜRK purchase only the finest raw material that will suite our clients needs.
Once the grower is ready to bring his harvest we provide the transportation in our own plastic crates. This means that we are able to create a hygienic conditions all the way through the process. Before the grower brings in his harvest he is asked to provide a one kilogram sample to the Purchasing Department. The sample is then graded and checked for the quality by the same department. If it is cleared the grower is then allowed to bring in the full lot. Once the full lot arrives at our facility samples are taken from different boxes. These samples are then compared with the initial sample that was brought in. If the samples match, the full lot is transported in to our insulated warehouse. The boxes from the same grower are given identification labels with the information of the grower, the delivery date and the region it was grown in. This labelling provides us with full traceability from the beginning of the process right to the end.
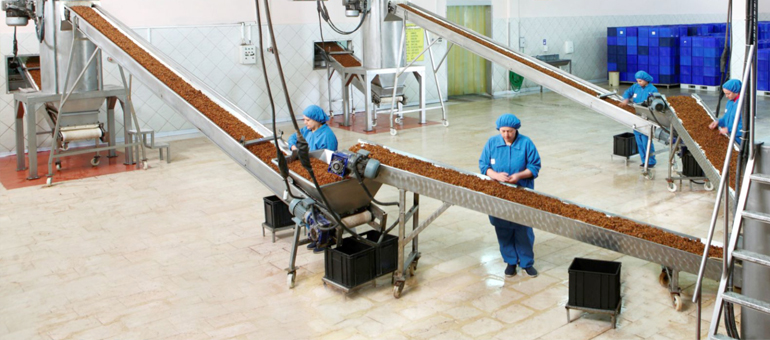
Our facility has 2,500 sqm of storage area with insulated ceiling to allow for a stable temperature. Our warehouse is also split in to two different areas. One of these is used for the storage of the conventional goods and the other is only used for the storage of the organic sultanas. This is done to eliminate the risk of cross contamination. ERTÜRK's storage facility, like the rest of our factory is checked twice a month by an independent Pest Control Contractor and once a week by our own Quality Control Department.
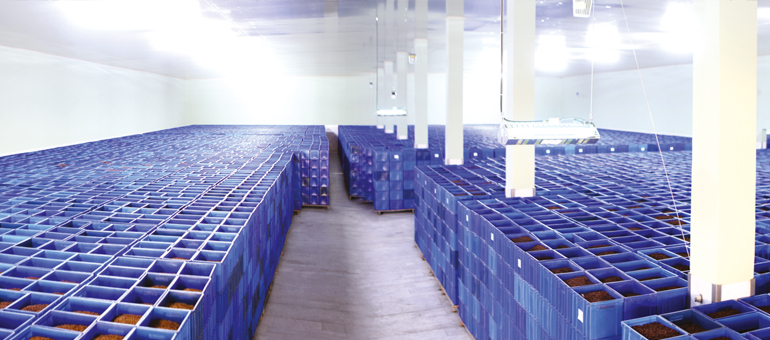
The first part of the process starts with the raw material being placed in to our Bulk Breaker. This is used to separate any clumping that may have occurred during the storage. Once the raw material has passed from the Bulk Breaker it is transported to the Dry Capstemmer via conveyor belts which pass under magnets to remove any metallic foreign material. The Dry Capstemmer utilises centrifugal force to remove the capstem which attached the berry to the bunch.
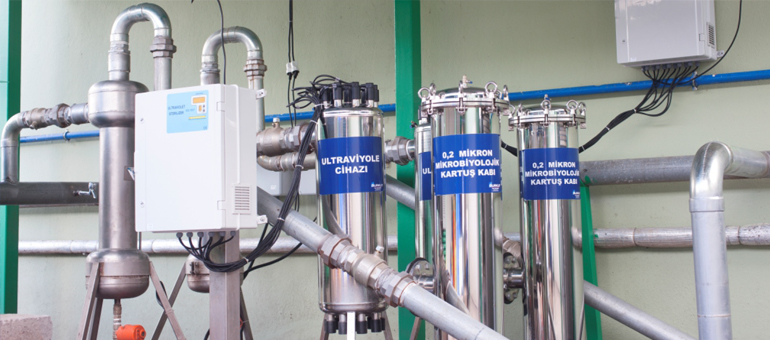
After this process is complete the sultanas are transported to the second part of our facility, the Washing Department.
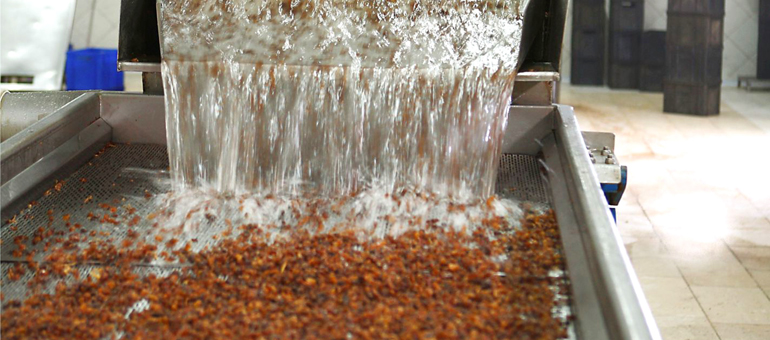
In the Washing Department of our factory the raw material is passed under several Aspirators which are there to remove any lighter foreign materials such as stems, branches and stalks.
After the Aspiration Process the sultanas are submerged in water which is sterilised by UV lights. In order to remove any heavier foreign material from the sultanas the sultanas are transported to the cascade washer via water pumps. This process uses the flow of water and the pull of the gravitational force to remove material such as Stones. To achieve the maximum level of cleaning the semi-processed material is Then placed in to the Wet Capstemmer. This process removes any capstems that may still be attached to the berry.
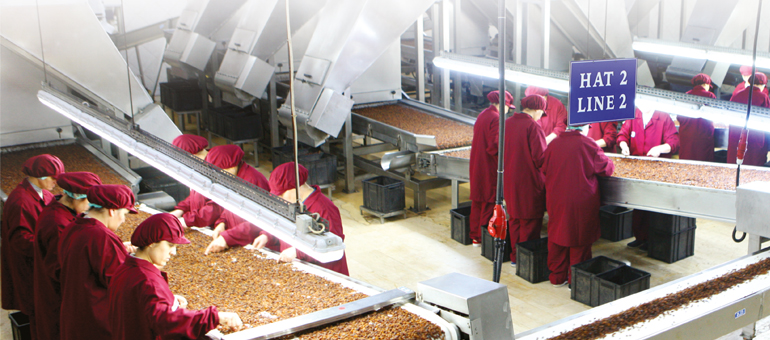
To get the best free flowing raw material the sultanas are passed under the Oiling Station. The oiling station applies oil to the sultanas. The oil used is specified by the customer specifications to the sultanas. Oils Used: Rapeseed, Cotton Seed, High Oleic Sunflower Oil And Organic Sunflower Oil.
After the oiling process the two different lines are split into four lines which once again pass under the aspirators. Due to ERTÜRK being a quality based company, before the sultanas pass in to the Mechanical Sorting Department the produce Flows past experienced workers who visually inspect the sultanas for any foreign material and non-conformaties in or on the sultana. Our Mechanical Sorting department is equipped with four Laser Scanners which are updated with the latest programming which also use different coloured laser beams that can identify different coloured foreign material and can also be used to sort out different colour berries in order to get the type we need.
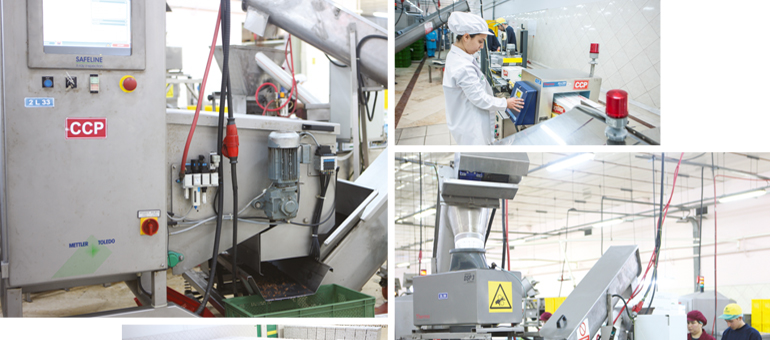
The sultanas that have passed from the Laser Scanners then go in to the X-ray scanners. The X-ray Scanners are used to identify any foreign material that may be embedded inside of the berry. A second function of the X-ray is to reject any Quarts Crystals in the product. This second function is used because, in some conditions due to reflective and refractive qualities of the Quarts Crystal the Laser Scanners have been known to miss these crystals. Once the X-ray scanners have cleared the sultanas they enter the final stage of our process. The Metal Detection and Weighing Station.
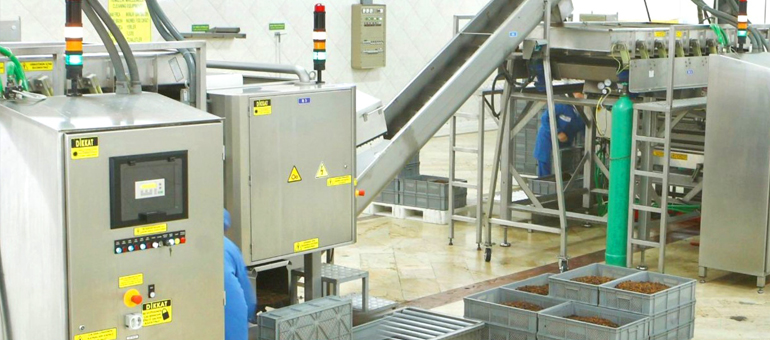
On the Metal Detection and Weighing Station the almost ready sultanas are passed through an Online Throat Metal Detector which then, if cleared, moves them on to the highly sensitive Weighing And Boxing Station. Once the boxes are filled to the correct weight they are closed and passed under an Online Case Metal Detector. This process is to identify any foreign metallic material that may have been in the cardboard box.